You might already be familiar with the properties of different types of stainless steel—such as how grade 304 stainless steel has excellent corrosion resistance or how annealed and stress-relieved 430 stainless steel has an incredibly high hardness. However, one common question that a lot of people have is: “How is stainless steel made?”
While Marlin Steel doesn’t manufacture stainless steel ingots or wires, the manufacturing team does work with stainless steel metal on a daily basis. Part of understanding how to work with different types of stainless steel is knowing how they’re made and how they can be modified.
So, here’s a quick explanation of how stainless steel is made.
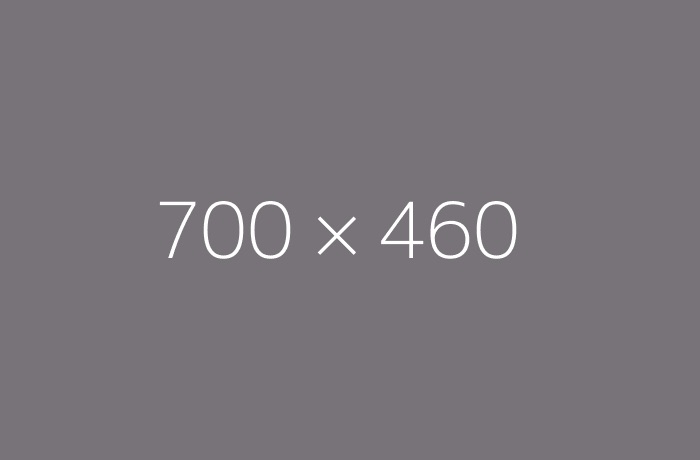
What is Stainless Steel?
Before explaining how stainless steel is made, it’s important to know what stainless steel is, and what makes it different from plain steel. At its most basic, stainless steel is an alloy of iron and several other elements (such as nickel, chromium, molybdenum, and carbon) that is more resistant to corrosion than plain iron or steel (which is simply iron and carbon).
These stainless steel elements, such as nickel, chromium, and other additives, give it a passive oxide layer that resists the formation of rust and creates a shiny, reflective surface. The shiny surface of stainless steel is very difficult to tarnish compared to plain steel, hence why it is called “stainless” steel.
Raw Materials
Stainless steel metal is formed when the raw materials of nickel, iron ore, chromium, silicon, molybdenum, and others, are melted together. Stainless steel metal contains a variety of basic chemical elements that, when fused together, create a powerful alloy.
Different proportions of stainless steel elements—iron, nickel, chromium, molybdenum, and carbon (among others)—determine the type of stainless steel. The ratio of iron to other materials affects how strong the protective oxide layer is, how resistant the metal is to specific corrosives, and a few other mechanical properties (hardness, melting point, shear modulus, etc.).
These differing ratios of stainless steel components produce the different types of stainless steel alloys. Each unique combination is referred to as a “grade” of stainless steel—such as grade 304 stainless, grade 316 stainless, or grade 420 stainless steel.
How is Stainless Steel Made?
First, when making stainless steel, the manufacturer has to determine exactly which type of stainless steel they want to make. This is important because the grade of stainless steel they want to make will affect the ratio of stainless steel materials that will be present in the mixture, such as iron, carbon, nickel, etc. These ratios aren’t always exact—sometimes, they’re on a range because of the inevitable risk of variance in the purity of each element in the mix.
The Manufacturing Process: How to Make Stainless Steel
Once the raw materials are gathered, the rest of the stainless steel manufacturing process can begin. Here are the basic steps:
- Melting the Raw Materials. The different stainless steel materials are placed in a furnace (typically an electric furnace for modern stainless steel manufacturing applications) and heated to their melting point. This process can take anywhere between 8 and 12 hours, according to metalsupermarkets.com and other sources. Once the metal is molten, stainless steel manufacturing can proceed to the next step.
- Removal of Excess Carbon. The molten material placed into a vacuum oxygen decarburization (VOD) or argon oxygen decarburization (AOD) system to remove excess carbon. Depending on how much carbon is removed, this process could result in a standard or a low-carbon variant of the alloy—for example, 304 versus 304L stainless steel. This can affect the tensile strength and hardness of the final product.
- Tuning or Stirring. To help fine-tune the quality of the final product, the molten steel may be stirred to help distribute and/or remove specific stainless steel components from the mixture. This helps to ensure that the stainless steel is of uniform quality and will meet the specifications required by end users (like Marlin Steel).
- Forming the Metal. As the stainless steel begins to cool, it is put through a variety of forming processes—starting with hot rolling while the steel is still above its crystallization temperature. Hot rolling helps get the steel into a rough shape, and is often used to create billets or blooms of metal. To create metal blooms or billets of precise dimensions, the stainless steel may be cold rolled.
- Heat Treatment/Annealing. To relieve internal stresses and alter the stainless steel’s mechanical properties, it may be annealed (heated and cooled under controlled conditions). If annealed, the steel may need to be descaled so the protective oxide layer isn’t compromised.
- Cutting and Shaping. After the annealing process, stainless steel is put through a variety of cutting and shaping processes to create an ideal final product for the application. The specific operations used to cut the stainless steel will vary depending on the size and shape of the billet/bloom and the desired final product. For example, the steel may be cut mechanically with large metal shears if making thick metal plates. Meanwhile, CNC punch or laser cutting machines may be used to cut shapes out of thinner metal sheets. Marlin Steel’s manufacturing team often creates custom metal cutouts from sheet metal plates by using cutting lasers and CNC punch machines.
- Applying Surface Finishes. The stainless steel manufacturer may apply different surface finishes to their stainless steel billets, blooms, or wires before shipping them to other manufacturers. The specific finish applied will vary depending on the steel’s intended use—but one of the most common surface finishes is simply grinding down the surface to remove impurities and make it smoother.
Quality Control
Before finishing a stainless steel basket or product, the engineers at Marlin Steel run finite element analyses on each and every design. For maintaining quality control, Marlin Steel employs a top-of-the-line FEA software from Autodesk because it provides incredibly accurate simulations in mere minutes—saving considerable time, labor, and materials compared to manual testing processes.
In this FEA analysis process, Marlin’s engineers can program the software to simulate different distributions of weight on the basket at different temperatures and after exposure to specific chemicals.
By testing these effects, the team at Marlin Steel can spot potential issues before finishing the job, ensuring the customer receives a stainless steel basket of the highest quality.
Stainless Steel Manufacturing at Marlin Steel
Marlin Steel does not manufacture stainless steel wires and sheet metal in-house. Instead, Marlin Steel works with a variety of stainless steel manufacturers in America to procure high-quality stainless steel alloys of all types on a moment’s notice. The Marlin Steel team is proud to work with American-made steel to craft 100% American-made custom wire and sheet metal baskets here in Marlin’s Baltimore, Maryland factory.
With high quality stainless steel materials, along with top quality control methods, Marlin Steel produces custom steel wire forms that are built to last for years.
Curious about how Marlin makes our stainless steel products? Or, do you need a custom wire form for your manufacturing application ASAP? If so, reach out to the Marlin Steel team today.